How It Works
RFID vs. AI in Logistics: Choosing the Right Technology for Your Operations
| Kargo | 4 min
What You Need to Know

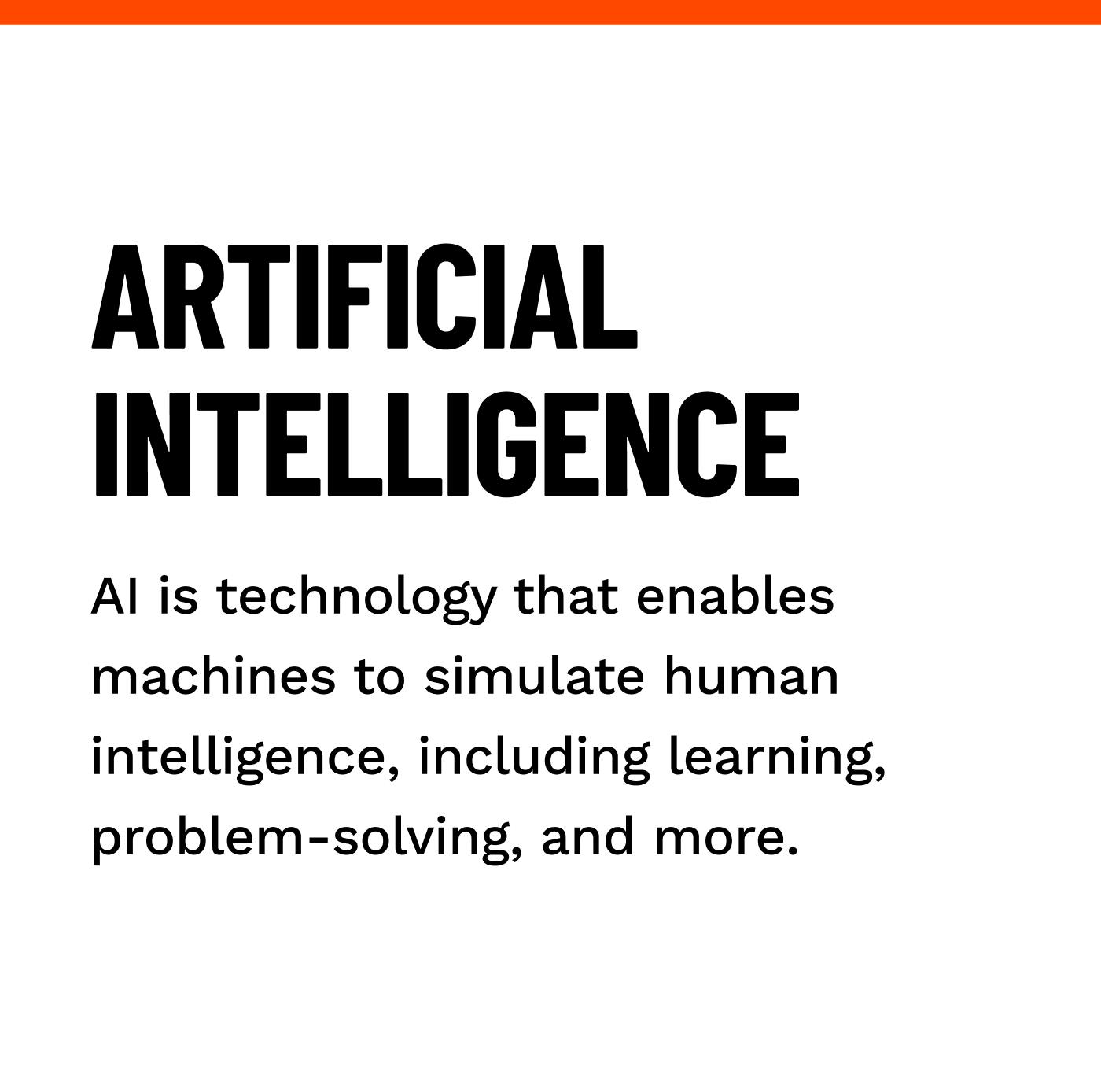
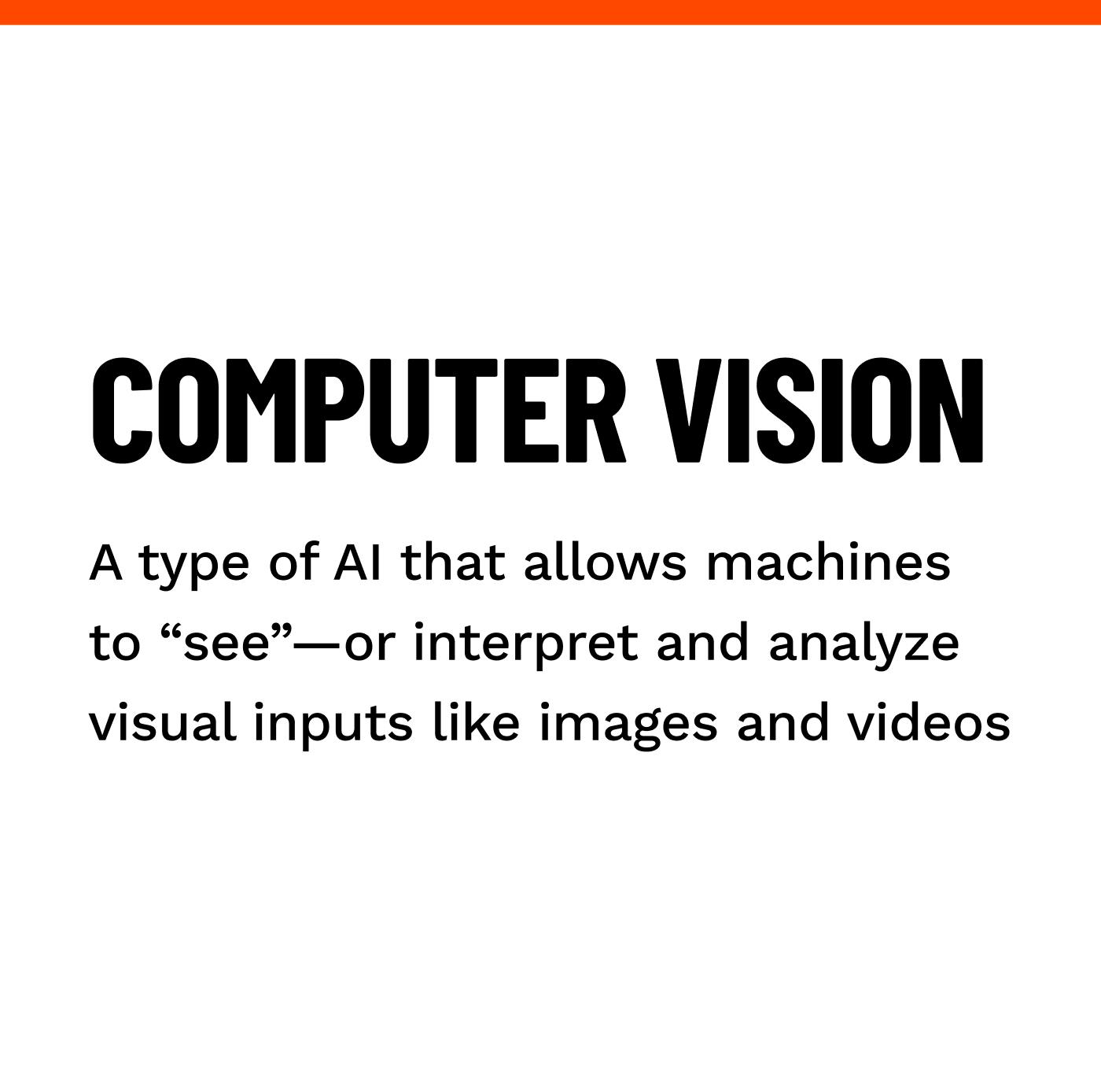
Radio Frequency Identification technology (RFID) has long been an invaluable tool in logistics, helping teams track inventory and streamline processes. But now, there’s a new technology on the scene: Artificial intelligence (AI). AI brings new possibilities, from real-time quality checks to predictive insights, that go beyond what RFID can offer. So how do these two technologies stack up? This post dives into the core capabilities of RFID and AI, exploring where each technology shines and how they address the unique challenges in modern logistics.
Understanding RFID in Logistics
RFID technology has long been a backbone in the warehousing world, allowing companies to track assets, reduce errors, and keep tabs on inventory without the need for constant manual intervention. For industries with high-volume shipping and receiving, RFID tags offer a powerful solution for asset tracking and inventory visibility.
Some of RFID’s strongest use cases include:
- Asset Tracking: From pallets to individual products, RFID tags enable precise tracking of items across warehouse facilities, reducing the risk of misplacement or loss.
- Error Reduction: RFID automates aspects of data collection, decreasing manual entry and the potential for errors.
- Inventory Management: RFID can streamline inventory counts, helping teams maintain up-to-date records without the need for time-consuming manual counts.
However, RFID alone has its limitations. While it’s excellent for tracking and managing data on tagged assets, it doesn’t provide information about the condition or quality of the items themselves. This is where AI plays a crucial role.
AI in Logistics: New Capabilities and Greater Insights
AI goes beyond basic tracking by analyzing images, video, and other data, providing visibility not only into where items are located but also into their condition, quality, and other potential issues.
Some key strengths of AI in logistics include:
- Condition Monitoring: AI can spot issues like damaged goods or poorly packed pallets, a must-have in sectors like food and beverage where quality is critical.
- Predictive Analytics: AI can analyze patterns over time to predict inventory needs, helping teams plan proactively and reduce waste.
- Labor Efficiency: By automating tasks that require human oversight, such as quality checks, AI can reduce the amount of labor required for routine tasks, freeing up employees for higher-value work.
- Scalability: Unlike RFID, which requires substantial infrastructure to expand, AI can be implemented flexibly across different facility setups and reconfigured as warehouse needs change.
In short, AI empowers warehouse operations with a depth of data and predictive insights that RFID alone cannot provide, making it an invaluable solution for organizations that prioritize visibility, efficiency, and accuracy.
Key Comparison – RFID vs. AI for Logistics
Now that we’ve outlined the capabilities of each technology, let’s compare them across common warehouse needs.
- Inventory Tracking: RFID excels in simple tracking, while AI takes it further by allowing teams to monitor inventory condition in addition to location.
- Quality Assurance: RFID provides location data but no insight into item condition. In contrast, AI’s ability to detect visible damage offers a strong advantage for industries that require frequent quality checks.
- Labor Efficiency: RFID reduces manual tasks by automating data capture, but it still requires manual intervention for many quality checks. AI, by automating quality inspections, allows teams to operate with fewer hands on deck.
- Scalability and Flexibility: RFID infrastructure can be costly and difficult to adapt to changing warehouse configurations, while AI’s adaptability allows it to fit into various facility layouts and scale more easily.
Which Technology to Choose Based on Logistics Challenges
So, which technology should logisics leaders prioritize? The answer depends on your specific needs. For basic inventory management, RFID can be an effective solution. However, for high-compliance industries like food and beverage and manufacturing, AI provides additional benefits that ensure quality, increase efficiency, and support long-term operational goals.
In some cases, combining both technologies offers the best results. RFID can serve as a foundation for inventory tracking, while AI builds on this foundation to deliver deeper insights and enhance quality assurance processes.
RFID and AI each have their place in modern logistics. Understanding their individual strengths helps leaders make informed decisions, ultimately enhancing facility operations and resilience in today’s fast-paced supply chain environment.
Questions?
Connect With us
Ask us anything or drop your email to stay in touch